Design for Manufacturability (DFM) in VLSI: Enhancing Yield and Performance
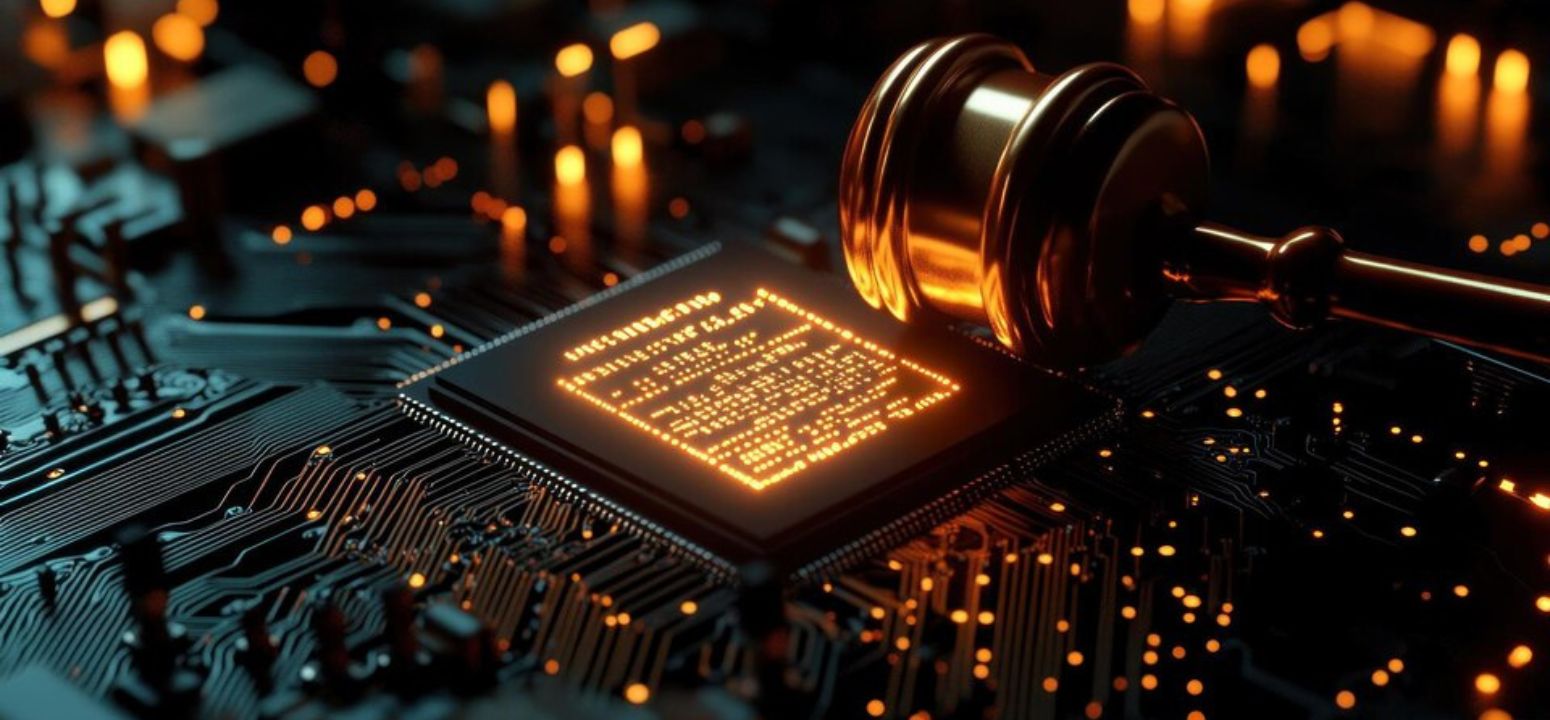
Introduction to Design for Manufacturability (DFM)
Design for Manufacturability (DFM) is a critical aspect of VLSI design that focuses on optimizing chip layouts to ensure high yield and performance during fabrication. With the increasing complexity of semiconductor devices, DFM techniques help in minimizing defects, improving reliability, and reducing manufacturing costs.
Importance of DFM in VLSI
As technology nodes shrink, variations in fabrication processes can lead to defects, yield loss, and performance degradation. DFM addresses these challenges by ensuring that designs are resilient to manufacturing variations. By integrating DFM techniques, designers can:
- Reduce defect rates
- Improve chip performance
- Lower manufacturing costs
- Enhance overall yield
Key DFM Techniques in VLSI
Several techniques are employed in DFM to optimize the manufacturability of VLSI designs. These include:
1. Layout Optimization
- Ensures that circuit layouts adhere to foundry-specific design rules.
- Reduces stress-induced defects and lithography issues.
- Enhances process uniformity to improve yield.
2. Design Rule Checking (DRC) and Optical Proximity Correction (OPC)
- DRC ensures that the design layout follows fabrication constraints.
- OPC compensates for lithographic distortions, ensuring precise patterning on silicon.
3. Redundant Via Insertion
- Helps in enhancing the reliability of interconnections.
- Reduces the probability of via failures, which can cause open circuits.
4. Dummy Fill and CMP Optimization
- Dummy fills balance the density of the layout to prevent chemical-mechanical polishing (CMP) issues.
- Ensures uniform thickness across the wafer, improving manufacturability.
5. Antenna Effect Mitigation
- Addresses plasma-induced charging damage during fabrication.
- Prevents gate oxide damage by incorporating antenna diodes or modifying metal routing.
6. Critical Area Analysis (CAA)
- Identifies regions in the layout prone to defects.
- Reduces the probability of random defects affecting chip functionality.
DFM and Advanced Nodes
With the advent of sub-10nm technologies, DFM has become more crucial than ever. Advanced process nodes require more stringent DFM methodologies, including:
- Machine Learning-Based DFM: Uses AI to predict yield and suggest optimizations.
- Computational Lithography: Enhances photomask designs for better pattern fidelity.
- Multi-Patterning Techniques: Addresses lithographic limitations in advanced nodes.
Conclusion
Design for Manufacturability (DFM) plays a vital role in ensuring that VLSI designs are production-ready with high yield and reliability. As semiconductor technology advances, DFM strategies continue to evolve, integrating more sophisticated tools and methodologies to tackle fabrication challenges effectively. By adopting robust DFM techniques, chip designers can significantly enhance the performance, reliability, and cost-effectiveness of their designs.